The DIY home renovation of "the cabin" began in 2020, just as the quarantine began. We built our own DIY furniture, home automation, and more. These are the projects and lessons we learned.
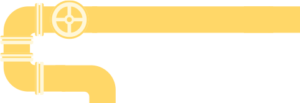
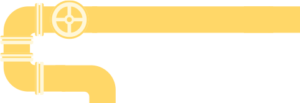
100% DIY home automation. From the thermostats to the security cameras, everything we used in designing our home was built on a budget. At the heart is Raspberry Pi home automation with Arduino sensors. Below are all of the IOT projects (networking, software, and hardware) that made this DIY home automation possible.
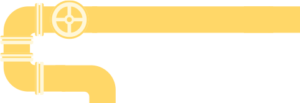
The DIY approach to decorating a home with furniture, accessories, and knick-knacks. From the large scale to the small, complicated to the hard—CNC router projects that are actually worth making.
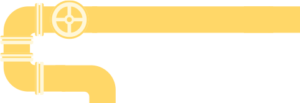
What we learned from building and living in a van, traveling the world over many years. Complete with my approach to crafting a wood-cabin theme, lessons from the road, and lots of pictures of our dog.
Latest articles
Types of Waterproof Cases IP67 enclosures and connectors are the most common and versatile for outdoor usage. The IP67 rating means that the waterproof case can handle up to thirty minutes in...
LEDs are delicate devices. Building art or home improvements that use outdoor lighting requires specialty equipment to protect from the elements. We've tried many such products in the most extreme...
Ever since I first built built the Maslow CNC Router (Classic), I've been anticipating the M2 upgrade kit. I have waited this long to do a real Maslow CNC review; after months of use, I can finally...
There are various upgrades to improve the performance of the Maslow CNC. It took many weeks of experimentation before I could use 100% of a piece of wood (yes, even the corners). Finally, we are able...
DIY hidden security cameras can complete a home CCTV system without sacrificing the look of a room. Cheap Arduino parts can be tucked away into a wall, window, or door to easily add a layer of...
A DIY home security camera is only as good as its ability to detect threats. Our CCTV system can detect people, cars, visitors, and more. Pictures are captured and presented for review.Machine...
Control a Pan Tilt Zoom Security Camera (MotionEye Actions) in Home Assistant
Home Assistant support for MotionEye cameras limited. I created a custom component with auto-discovery and actions for my pan tilt zoom security camera. You can find the Home Assistant MotionEye...
After a few weeks with our Maslow CNC router, we graduated to using nicer wood to make real furniture. CNC cabinets are a great beginner woodworking project. They take advantage of the precise...
Building a DIY Raspberry Pi security camera is much easier than it might sound thanks to open-source security camera software. We use several such cameras placed around the house, as part of our DIY...
The Maslow CNC router is popular because it is large, open-source and cheap. It is uniquely well-suited in the CNC space for making furniture on a budget. This made it the ideal choice in my attempts...
Menu
Related & Recent…
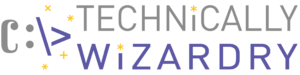